Original Equipment Manufacturers (OEMs) play a crucial role in multiple industries. These industries are rapidly evolving and changing, creating a dynamic environment for skills and training.
As the demand for high-quality products and services continues to grow, skilled professionals in extended enterprises must stay abreast of the most current technology and trends. To ensure competence and maintain industry standards, accrediting skills within extended enterprises has become a vital practice.
Skill accreditation involves recognizing and certifying the competencies of individuals working within OEMs and their partner networks. This process aims to validate the skills, knowledge, and expertise of professionals, ensuring they meet industry-specific standards, which is the definition of extended enterprise training.
Accreditation not only enhances the credibility and reputation of OEMs but also fosters partner and customer confidence and trust in their products and services. By accrediting skills, OEMs can ensure that their workforce possesses the necessary qualifications and capabilities to deliver excellence consistently.
You are operating a training program in an industry where technological advancements occur at a rapid pace. To keep up with these advancements, skill accreditation processes must be designed to encompass the latest technologies and practices. This requires continuous evaluation and updating of accreditation standards and criteria.
Challenges of Managing Accreditation
With the spread of vast enterprise networks that are common with OEMs, it can be challenging to ensure that all technicians are maintaining accreditation. With multiple locations, roles, and product lines, and the number of employees needing to maintain accreditation – it can often feel impossible in the face of an ever-evolving industry.
You are operating a training program in an industry where technological advancements occur at a rapid pace. To keep up with these advancements, skill accreditation processes must be designed to encompass the latest technologies and practices. This requires continuous evaluation and updating of accreditation standards and criteria.
In addition to technology, market demands and customer preferences in the industry are subject to frequent shifts. Skill accreditation processes must adapt to these changes to ensure that professionals possess the necessary skills to meet evolving market needs. Continuous professional development programs can help individuals update their skills and maintain their accreditation.
OEMs and extended enterprises often operate on a global scale, working with diverse suppliers, partners, and customers. Managing skill accreditation becomes complex and frustrating for training managers when dealing with different regulatory frameworks, regional variations, and cultural differences.
A standardized accreditation process recognized internationally can help mitigate these challenges and maintain consistency across operations. By tailoring the training program of your organization to accommodate this process, you can alleviate some of the frustration of maintaining accreditation.
So what are some of the ways that you can keep the employees of your enterprise accredited? It all comes down to having a plan and staying ahead of the changes in the market to ensure your technicians are prepared.
Best Practices for Managing Accreditation
There are many strategies that can be implemented to manage accreditation on the scale of an extended enterprise. It ultimately boils down to planning, organization, and assessments for skill gaps in your current training program.
Leveraging Collaboration
Collaboration with industry associations, trade organizations, and regulatory bodies can assist with developing accreditation frameworks that align with industry standards. By incorporating these frameworks into the individual training plans across your network, you can ensure that technicians have access to the training they need to achieve or maintain accreditation.
By involving the key stakeholders that set the terms for accreditation, you can keep ahead of market trends and ensure that your accreditation criteria are comprehensive, up-to-date, and relevant to the industry’s needs. This will give you plenty of time to prepare your technicians for changes that may come their way and impact their current accreditation.
Encouraging Professional Development
Encouraging and supporting the continuous professional development of your technicians is vital. By keeping your technicians current on your products and engaged in the industry and developing market trends, you can stay one step ahead in helping them achieve and maintain their accreditation status.
This can be achieved through training programs, workshops, seminars, and online courses. OEMs can also partner with educational institutions and training providers to offer relevant skill development opportunities, enabling employees to enhance their expertise and maintain their accreditation.
Regular Performance Evaluations and Feedback
Performance evaluations and feedback mechanisms are critical for identifying skill gaps and areas needing improvement. By holding consistent performance evaluations that measure technician performance against business key performance indicators (KPIs) and industry standards, you can gauge whether your training program is setting technicians up for success on their path to accreditation.
OEMs can implement performance management systems that provide employees with constructive feedback and guidance in response to their evaluations. By providing additional resources that can help fill the gaps of your technicians, you can help them align their skills with industry requirements.
Leveraging Technology
Leveraging technology for assessments that are associated with accreditation can streamline the accreditation process for your technicians. Online platforms, simulation tools, and virtual training environments can be utilized to assess practical skills and capabilities effectively.
Using the different resources that technology can provide is a huge benefit to extended enterprises with a global presence. These tools enhance the efficiency of the delivery of training materials and enable remote assessments to facilitate the accreditation process globally.
The Solution to Managing the Dynamics of Accreditation
With the aforementioned strategies, you can simplify the way you manage the accreditation of your network. While these strategies simplify the process, staying organized and keeping on track becomes the next challenge.
That’s where LatitudeLearning comes into play. The LatitudeLearning LMS specializes in managing the accreditation of skills across your enterprise. Once technicians have been trained, performance metrics can be brought in to measure the competency of the skills.
When competency is aligned with appropriate KPIs, accreditation is achieved. LatitudeLearning LMS supports your enterprise’s ability to monitor training status, completion, and performance against specified metrics and KPIs.
The industry throws a curve ball at maintaining accreditation because, as skills atrophy and requirements change, the definition of accreditation or certification also changes. There are many LMS options that mark skills as static and that don’t account for these changes.
LatitudeLearning understands the dynamic nature of skills and certifications and understands that you need an LMS that can manage them, especially at the enterprise scale. Check out LatitudeLearning’s guide to Extended Enterprise Training.
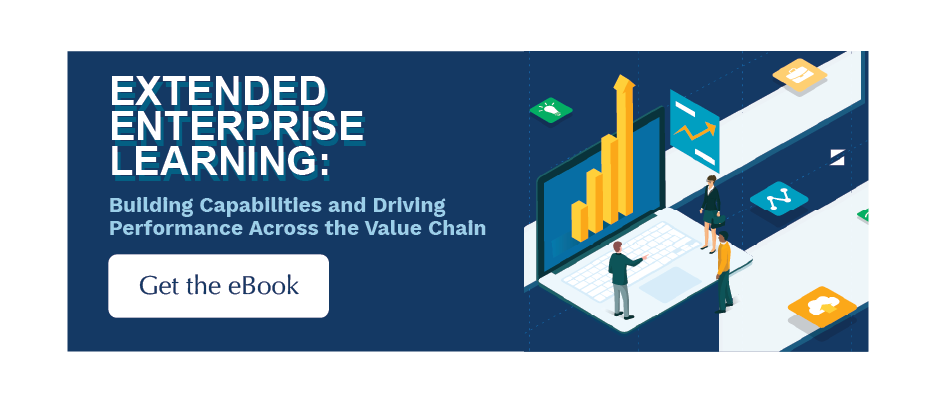
[…] strict mandates in place that forced many jobs to adapt to virtual working environments to replace hands-on training, workshops, and seminars, many skills were not mastered in the way that they normally would have been – exacerbating […]